I am text block. Click edit button to change this text. Lorem ipsum dolor sit amet, consectetur adipiscing elit. Ut elit tellus, luctus nec ullamcorper mattis, pulvinar dapibus leo.
Engineering
Using 3D scanning for engineering is the fastest and most cost effective way to make alterations to an existing part or product. The traditional method of taking measurements with a calipers to create a 3D model from scratch is both time consuming, and often inaccurate for items with complex curves and designs.
Our Scanner
Our Artec scanner captures huge amounts of cloud point data to an accuracy of 0.05mm. Using specialised software, this data is fused into a high polygon mesh with a resolution of up to 0.1mm. This mesh can be exported in an 3D file format such as obj. or stl., ready for 3D printing, visualisations, and quality control analysis.
Converting the Scan Mesh
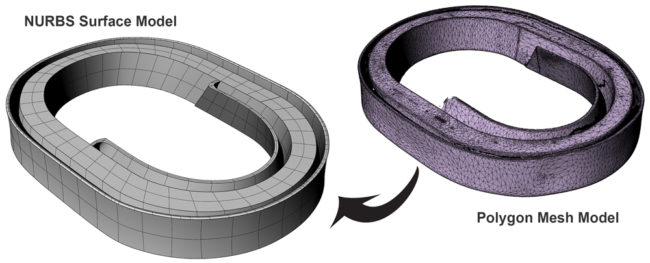
For reverse engineering purposes it is usually desirable to have the high poly mesh converted into a NURBS model format so it can used in a 3D CAD program such as Solidworks. While it is possible to make slight alterations to the polygon mesh without converting it to a nurbs surface, you will be limited to minor fixes. When more accurate or demanding changes have to be made you must convert the mesh. Converting the polygon mesh model to a NURBS model is a manual process of modelling around the scan to create a clean, solid object with a perfectly smooth surface finish. We use deviation analysis software to ensure that the new solid model is accurate to the original scan. Finished files are manufacture ready and can be used for 3D printing or for technical drawings. These files can be exported as STEP, IGES, Parasolid and more. We offer this additional file conversion service as an add-on package to having an object 3D scanned.
Quality Inspection
The accuracy and high resolution of our Artec Spider blue laser scanner makes it the perfect tool for quality inspection and quality control. It quickly and precisely captures the intricate 3D form of entire small objects or the complex details of larger objects.
Our scanner is able to recreate every part of an object, from sharp edges to the geometry of a surface, and every tiny detail in between. The resulting 3D model can be superimposed onto the original 3D CAD design, allowing a detailed comparison between the “as made” and “as designed” models. This is a fast and efficient way to ensure that there are no faults in a part before, during or after production
The Process
After we post-processes the captured cloud point data, fusing it into a highly accurate polygon mesh representation of the original scanned object, we export the model into our deviation analysis software. With the 3D Scan and original 3D CAD model overlayed we can directly draw a comparison between them, measuring any variations within a given tolerance, and producing a clear and definitive deviation map.
This map can be utilised as tool to immediately conclude whether a part has any defects, is accurate to the original model ,and verify the compliance of the manufactured part’s quality.
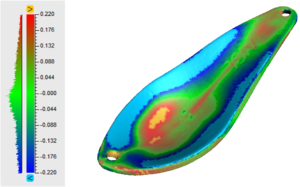
Deviation Analytics
Film & TV
3D scanning provides an excellent substitute to some traditional processes used in prosthetics, prop making and practical effects in film production. Not only can 3D technology achieve greater accuracy and definition, but it can do so more quickly and efficiently with much reduced fuss.
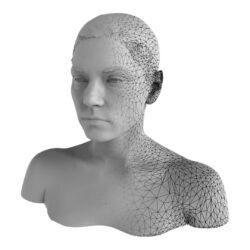
I am text block. Click edit button to change this text. Lorem ipsum dolor sit amet, consectetur adipiscing elit. Ut elit tellus, luctus nec ullamcorper mattis, pulvinar dapibus leo.
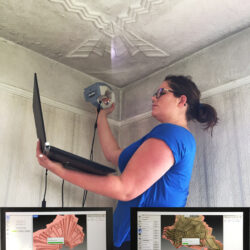
I am text block. Click edit button to change this text. Lorem ipsum dolor sit amet, consectetur adipiscing elit. Ut elit tellus, luctus nec ullamcorper mattis, pulvinar dapibus leo.